Electrocoating
Opposites Attract
Electrocoating, otherwise known as “E-Coat,” is a method of painting which uses electrical current to deposit the paint. The process works on the principal of “Opposites Attract” – materials with opposite electrical charges attract each other.
In this system, electrodes in the coating tank create positively charged paint particles which are attracted to the negatively charged part.
The paint particles are drawn to the metal part and paint is deposited on the part, forming an even, continuous film over every surface, in every crevice and corner, until the coating reaches the desired thickness. At that thickness, the film insulates the part, so attraction stops and electrocoating is complete. SPCI utilizes cathodic electrocoating, available in medium gloss black epoxy.
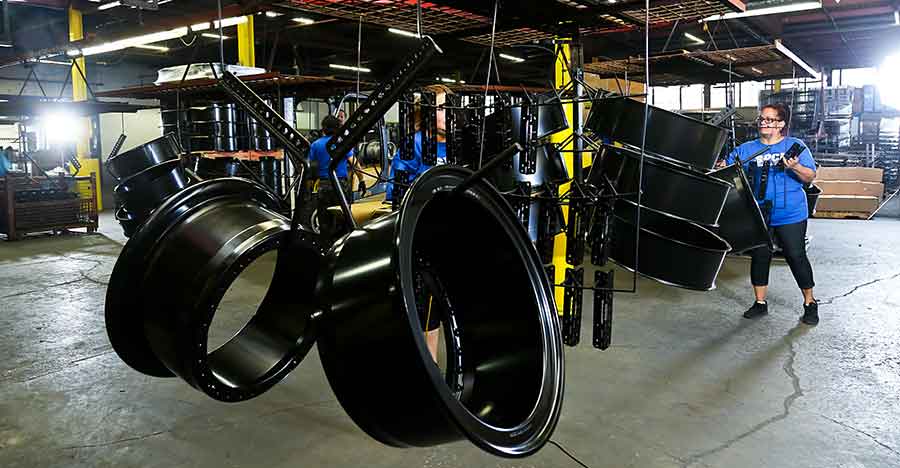
Materials That Can Be Electrocoated
- Cold Rolled/Hot Rolled Steel
- Galvanized Steel
- Iron Castings
- Zinc Castings
- Copper/Brass
- Conductive Composites
- Aluminum Extrusions and Castings
- NiZn Plated Steel
- Stainless Steel
- Chrome Plate
Thorough Treatment: Powder coating provides superior edge coverage. Since powder coated parts have virtually no drips, runs, or sags, the reject rate is very low. In addition, part to part color consistency is held to a tolerance which is not visible to the naked eye.
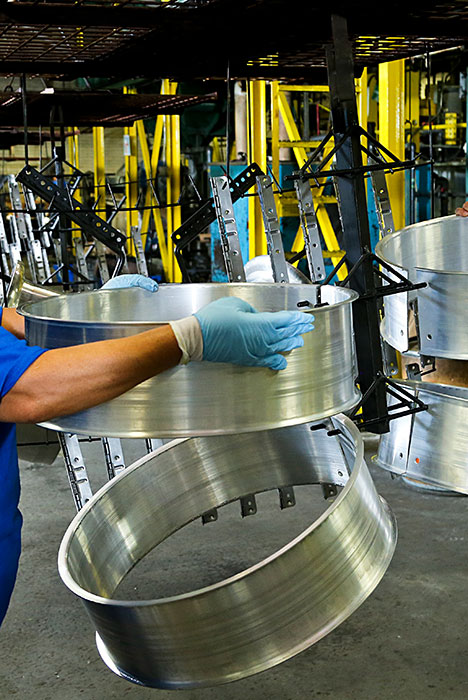

Benefits of Electrocoating
Environmentally friendly: Unlike most liquid coatings, there are no solvents to evaporate in the E-coat process. E-coat emits virtually no VOCs into the air, thus minimizing the impact on the environment. Also, any excess e-coat deposited or carried by the part is rinsed, reclaimed, and recycled to the electrocoat tank.
Outstanding Performance: Electrocoating provides an extremely chemical and corrosion resistant finish. Depending on the application, it can be used as a single coat application or a base coat. Electrocoating also provides an excellent base for a variety of top coats. This “dual application advantage” creates a more decorative and durable finish.
Adaptable for complex products: Electrocoating readily conforms to multifaceted configurations and yet maintains engineered tolerances on parts ensuring intended operating functions. Some examples include: internal surfaces, deep recesses, weldments, fasteners, small parts, and large parts, all of which receive uniform coating (no sags or runs).
The Electrocoat Process Can Be Divided Into Four Distinct Zones:
The pretreatment zone cleans and zinc phosphates the metal to prepare the surface for electrocoating. Cleaning and zinc phosphating are essential to achieving the performance requirements desired by today’s end user of the product.
The Electrocoat bath is where the coating is applied. The electrocoat bath consists of 80-90% deionized water and 10-20% paint solids. The deionized water acts as the carrier for the paint solids which are under constant agitation. The solids consist of resin and pigment. Resin is the backbone of the final paint film and provides corrosion protection, durability, and toughness. Pigments are used to provide color and gloss.
The post rinses provide both quality and conservation. During the electrocoat process, paint is applied to a part at a certain film thickness, regulated by the amount of voltage applied. Once the coating reaches the desired film thickness, the part insulates, and the coating process slows down.
As the part exits the bath, paint solids cling to the surface and must be rinsed off to maintain efficiency and aesthetics. The excess paint solids are called “drag out” or “cream coat.” These excess paint solids are returned to the tank to create a coating application efficiency above 95%.
The bake oven receives the parts after they exit the post rinses. The bake oven cross links and cures the paint film to assure maximum performance properties. Our typical bake cycle is 50 minutes at 400 degrees.
Call SPCI: 908-351-8707
Powder Coating • Electrocoating • ISO 9001 Certified
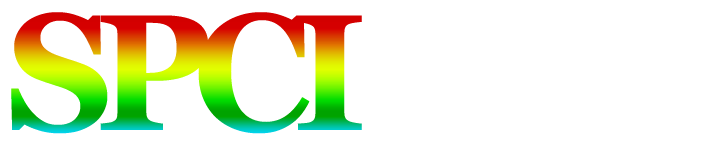
© Superior Powder Coating Inc. – All rights reserved. Site design by D2P Web Design.